When selecting a flex PCB manufacturer, there are a few things to remember. These factors include trace width, dimensions, stiffener, copper plating, and quality testing. When choosing a flexible printed circuit manufacturer, these details can make all the difference.
Dimensions
Depending on your needs, a flex PCB manufacturer can produce double-sided and multilayered boards. Double-sided flex PCBs can have more layers and better connections than standard FR4 circuit board designs.
When calculating the dimensions of a flex PCB, you should consider whether the dimensions are flexible or rigid. Typically, a flexible circuit has a single conductive layer made of copper between two layers of dielectric material. The base film must contain holes that allow the component leads to pass through. If your design requires a thin base film, you can opt for an FR4-based flex PCB.
Trace Widths
If you need to choose a flex PCB manufacturer, you must consider trace widths. Besides being a design factor, trace width can also directly impact the size of your PCB. Moreover, a good trace width ensures the proper functioning of the traces, thus ensuring maximum PCB functionality. Trace widths are determined by two factors – the purpose of the trace and the location on the PCB.
Stiffener
A reliable PCB stiffener manufacturer is crucial for your printed circuit board production. This part of the PCB is essential for the quality and cost of your finished printed circuit board. In addition, a reputable manufacturer will provide excellent support for your production from the design stage to delivery. To choose the right PCB stiffener manufacturer, check the following features. They should have multiple product lines and offer diverse services.
The PCB stiffener plays an essential role in the design process. A proper stiffener can eliminate excess heat and stress from the other components on the board, preserving the board’s overall function and design. It can also increase the board’s flex curve, adding additional support to brittle areas. It also ensures the integrity of the solder joints. Stiffeners can be found in various materials, ranging from polyimide to abrasion-resistant polyurethane.
Copper Plating
The metallization process for copper on flex PCBs involves chemical plating and depositing. The copper layer is also referred to as Cuposit. The through-hole plating on a flex circuit is typically 1 mil thick and should be a minimum of half a mil thick to provide mechanical support. By comparison, a typical rigid PCB may only have a 1/2 mil cuposit.
Next, copper is deposited onto the film surface of the flex PCB by applying a photosensitive etch resist. The film is then exposed and developed using the desired mask pattern. This process results in a thin layer of copper being deposited onto the flex circuit.
The process of copper plating is important for the success of flex PCB manufacturing. First, the conductive ink is filled into the via after drilling. Then, it is electroless plated and then sanded. This process produces a copper-filled hole with a reasonably flat surface. Finally, this copper layer is imaged, developed, and stripped of tin. Copper plating is one of the most critical steps in producing rigid-flex PCBs.
Quality
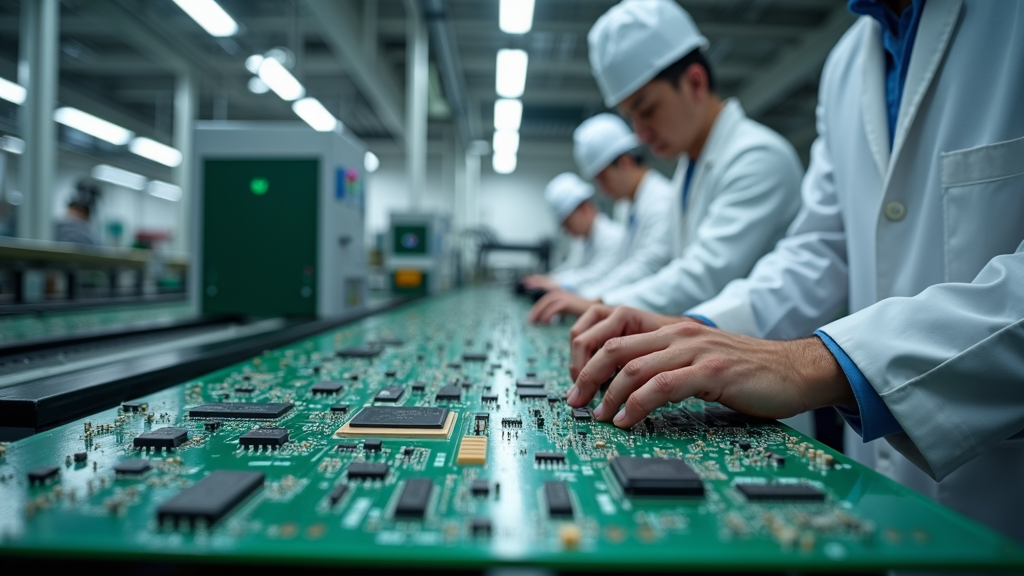
When selecting a flex PCB manufacturer, quality is key. The manufacturer should be able to meet the minimum order quantity of around four thousand to five hundred pieces per reel. There are three important assembly inspections for printed circuit boards.
The first inspection is a visual observation, and the second and third inspections involve testing soldered components. The inspection report will give a clear idea about the quality of the PCB manufacturing process. The PCB manufacturing company should have the primary stock of components such as resistors, capacitors, and inductors.
A high-quality flex PCB manufacturer will offer both rigid-flex and flexible circuits. Its extensive fabrication capabilities include the production of TFT-LCDs, which are thin film transistor liquid crystal displays.